Choosing the Right Abrasive Product for Welding and Metal Fabrication
You already know that you need to choose the right abrasive and use it properly if you want to minimize your costs and maximize your output when you're welding or fabricating metal. It's all too easy to grab whatever abrasive is handy when you're in a rush or have a deadline to meet, but using the wrong abrasive for your machine or ignoring safety rules can be risky. The results? Lower-quality finished products, increased costs and lost productivity. No one wants any of that.
So how do you choose the right abrasive for specific tasks? Glad you asked. Look at these tips and at the table here to make the right choices and use your grinding wheels and discs safely.
CUMI AWUKO Abrasives GmbH
Right Choices Matter –What is the Right Choice for Your Operation?
Abrasive products come in various levels of performance, which Awuko conveniently labels "good," "better" and "best."
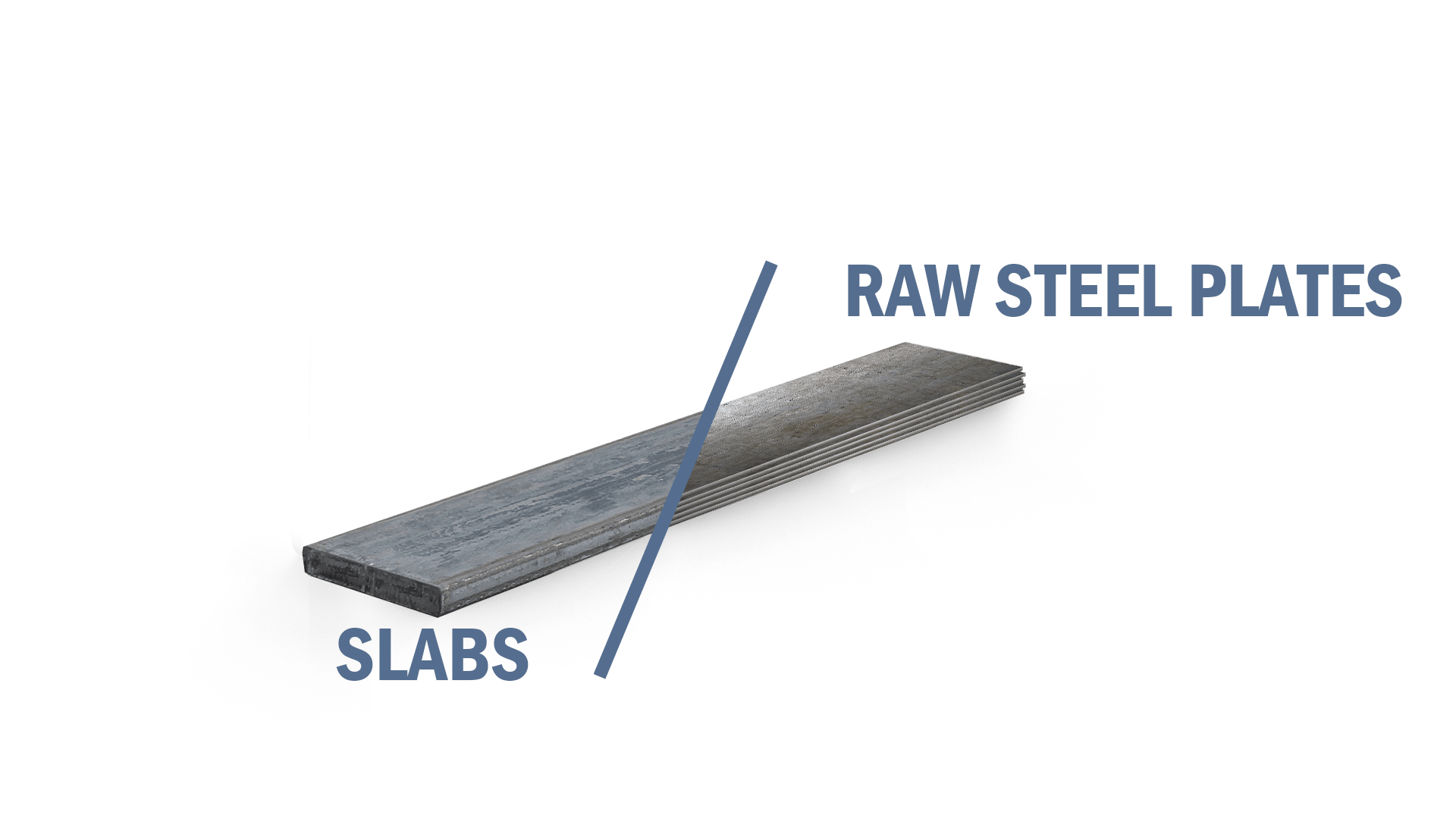
Which should you choose? Your choice involves balancing the results you want with the cost you're willing or able to pay. If initial price is your primary consideration, choose good abrasives, but be aware that a lower purchase price up front may not end up being economical in the long run. When you're running high-productivity applications and have to keep initial abrasive prices in mind, it's time for better abrasives. Consider the best abrasive products when maximum productivity and lowest total cost are critical to your operation.
When testing abrasive products to determine the best solution for your operation, there are three objective measurements to consider; one of which must remain constant between products being tested. These measurements are time, material removed, and product wear. By holding one of these constant and measuring the other two, you can come up with an objective comparison between multiple products. For example, you could grind for 10 minutes with each product, and measure how much material was removed and how much of the abrasive products were lost; this is often measured by weight. Alternatively, you could run each product to the end of its life, while measuring how much material it removed, and how long it lasted. Finally, you could remove a set amount of material while measuring the time and abrasive wear. Each business has unique priorities; following these test methods will allow you to select the right choice to meet yours.
Abrasive Selection Guide
Take a look at this chart when choosing an abrasive for welding and metal fabrication. Each application lists the relevant products in the order of best, better and good.
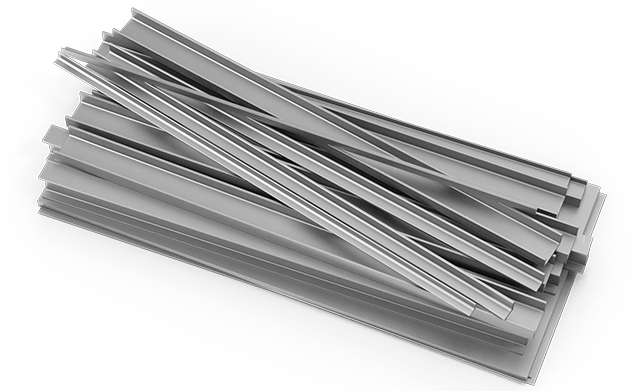
Grinding down metals
APPLICATION |
ABRASIVE PRODUCTS |
FORMULATIONS |
Cut-off applications:
- Cutting sheet metal
- Cutting, notching pipe
|
Cut-off wheels |
- Ceramic aluminum oxide and zirconia alumina blend for stainless and carbon steels, other ferrous and exotic metals
- Zirconia alumina for stainless and carbon steels and other nonferrous metals
- Aluminum oxide blend for carbon steels
|
Grinding:
- All weld grinding
- Pipe notching, beveling
- Heavy stock removal
|
Depressed center grinding wheels (24 or 36 grit) |
- Ceramic aluminum oxide and zirconia alumina blend for stainless steel and other ferrous metals
- Mix of zirconia alumina and premium aluminum oxide grains for metals ranging from alloys and stainless steel to gray iron and non-ferrous metals
- Aluminum oxide
|
Blending:
- Blending welds
- Medium to light stock removal
|
See-through fiber discs (24 or 36 to 80 grit) |
- Ceramic alumina for stainless steel and other ferrous metals
- Ceramic and zirconia blend for low pressure grinding of ferrous metals.
- Zirconia alumina for ferrous and non-ferrous metals
- Aluminum oxide for ferrous metals
|
- Blending welds
- Metal fabrication
|
See-through fiber discs (24 or 36 to 80 grit) |
- Ceramic alumina for difficult-to-grind materials, including super alloys and hardened steel
- Zirconia Alumina for fast stock removal and rough cutting applications
- Aluminum oxide blending disc for a consistent finish
- Aluminum oxide for general purpose applications
|
- Dimensioning and shaping
- Heavy stock removal
|
Coated abrasive cloth belts (for bench stand grinders) |
- Ceramic alumina for hard-to-grind alloys
- Zirconia alumina blend for exotic and heat-sensitive metals
- Zirconia alumina for stainless steelh
- Aluminum oxide for general use and maintenance/repair operations
|
Blending the surfaces
APPLICATION |
ABRASIVE PRODUCTS |
FORMULATIONS |
Deburring welds |
Coated abrasive flap discs (60 or 80 grit) |
- Ceramic alumina
- Zirconia alumina blend
- Aluminum oxide
|
Light deburring and finishing |
Resin fiber discs (80 to 120 grit) |
- Ceramic alumina
- Zirconia alumina blend
- Ceramic zirconia blend
- Aluminum oxide
|
- Blending and leveling (contours or flat surfaces)
|
Coated abrasive cloth discs (80 to 120 grit) |
- Ceramic alumina for a broad range of nonferrous applications
- Zirconia alumina for fast, cool cutting
- Zirconia alumina for stainless steel
- Aluminum oxide
|
- Blending
- Finishing
- Polishing
|
Cotton fiber depressed center grinding wheels may be used for light stock removal and finishing in one operation (24 grit for blending; 36 grit for finishing) |
- Cotton fiber combined with abrasive and flexible bonding material is especially good for bronze, aluminum and thin sheet steel
|
- Blending welds
- Deburring
|
See-through fiber discs (60 to 120 grit for light deburring) |
- Ceramic alumina for difficult-to-grind materials
- Aluminum oxide blending disc for a consistent finish
- Aluminum oxide for general purpose applications
|
- Surface preparation
- Blending welds
|
Coated abrasive cloth belts (120 grit) |
- Ceramic alumina
- Zirconia alumina blend for exotic and heat-sensitive metals
- Zirconia alumina blend for stainless steel
- Aluminum oxide
|
- Blending welds
|
Coated abrasive flap wheels (80 to 120 grit) |
- Ceramic alumina
- Aluminum oxide
|
- Cleaning
- Polishing
- Blending scratch patterns
|
Non-woven discs specifically for surface finishing (Medium, 120 grit) |
- Aluminum oxide
|
Creating the final finish
APPLICATION |
ABRASIVE PRODUCTS |
FORMULATIONS |
|
Non-woven, surface-finishing discs (Medium, 120 grit, or fine, 320 grit) |
- Aluminum oxide
|
- Weld polishing
- Cleaning
- Finishing
- Blending weld areas on stainless steel
|
Surface-finishing convolute wheels (Medium, 120 grit) |
- Silicon carbide
|
|
Depressed center grinding wheels (24 or 36 grit) |
- Aluminum oxide
- Silicon carbide
|
How to Use Abrasives Safely
The first step in using any grinding product safely is choosing the right abrasive product for each machine. Check the manufacturer's catalog to see what products are designed for which machines. Some catalogs use icons to make the machine-to-abrasive match clear and easy.
Check the product packaging as well. It's tempting to ignore product packaging, but it provides a wealth of information, especially about safety. Read and follow the safety information on the product packaging, and mount it on your machine so your operators always have access to it.
Basic tips for using and maintaining abrasive products and machines safely include:
The first step in using any grinding product safely is choosing the right abrasive product for each machine. Check the manufacturer's catalog to see what products are designed for which machines. Some catalogs use icons to make the machine-to-abrasive match clear and easy.
Check the product packaging as well. It's tempting to ignore product packaging, but it provides a wealth of information, especially about safety. Read and follow the safety information on the product packaging, and mount it on your machine so your operators always have access to it.
Safety Tips
- Don't grind near flammable materials.
- Grind and sand in well-ventilated areas whenever possible.
- Wear eye and face protection when working with any abrasive products.
- Wear a dust mask or approved respiratory protection. Check the packaging for the materials you're abrading or grinding to see which is recommended.
- Wear hearing protection. Pay attention to the noise exposure, and make sure you're protected when it exceeds established threshold levels.
- Wear safety gloves.
- Pay attention to where sparks are flying. Direct sparks away from your body and away from anyone else in the room.
- Don't wear loose-fitting clothing while grinding. Wear long-sleeved shirts or arm guards and long pants.
- If the tool you're working with starts to chatter or vibrate, stop at once. Find the cause of the problem, and fix it before you go any further.
- Use your abrasives on a first-in, first-out basis. Rotate your stock to keep the oldest abrasives ready at hand.
Grinding Wheel Tips
- Store your grinding wheels in a dry environment. Don't subject them to near-freezing temperatures or to dramatic temperature changes.
- If a wheel is cracked, chipped or otherwise damaged, don't mount it. If it has been dropped, don't mount it.
- Make sure that guards and work rests are all properly adjusted and secure before you start work. Safety guards should cover at least half of the wheel.
- Let a newly mounted wheel run for at least one full minute before grinding with it. Don't let anyone stand in front of or in line with the wheel during this time.
- Make sure flanges are clean, flat and free of burrs.
- Don't overtighten the flange retaining nuts.
- Compare the safe maximum operating speed of your grinding wheel with that of your grinder. Don't use a grinding wheel whose top-rated speed is less than the grinder's speed. Never exceed a grinding wheel's maximum operating speed.
- Never use a high-speed air sander with a grinding wheel. The speed of these pistol-grip air sanders far exceeds the maximum operating speed for grinding wheels. The result can be a potentially lethal wheel breakage. Many tragic injuries have resulted from using these high-speed sanders with grinding wheels. Don't let the next one happen on your watch. Instead, if you're using a high-speed air sander, only use sanding discs designed for the sander.
Fiber Disc Tips
- Store abrasive discs at the correct temperature and humidity: 60 to 80° F (15 to 29°C), and 40 to 50% relative humidity.
- Store coated abrasive discs properly. Keep them at least 4 inches (10+ cm) above the surface of concrete floors. Keep them away from open windows or heat sources and out of direct sunlight. Store them in their original packaging.
- If you receive an abrasive disc with damaged packaging, return it to the manufacturer. Don't use the disc.
- Check coated abrasive discs for damage before use. If you see any nicks, cuts, tears or other visible damage, don't use it.
- Never use a disc that has curled "sand side in" due to excess humidity. Edges of the disc not in full contact with the backup pad create a hazard when grinding.
- Never alter the size or shape of an abrasive disc or its back-up pad.
- Start up the tool just off the workpiece, and bring it up to full operating speed before you actually begin to grind or sand.
- As you start to grind or sand, ease the fiber disc onto the workpiece at a 5- to 10-degree angle to the piece's surface.
- If you're using a see-through disc or one with scooped holes, make sure nothing's protruding through any of the holes before you start up your equipment.
We all want higher productivity and lower cost, but safety comes first. Start by making sure your operators use their grinding and sanding equipment as if their lives depend on their safety precautions. Then use the correct abrasive products to get the job done right.